The right ERP can make or break your company’s growth

Many breweries get to the point where growth and expansion is the next logical step, but struggle with finding a way to lean into that growth without sacrificing the quality and customer experience that helped them get to this milestone.
An ERP touches virtually every aspect of your business, and choosing the right one can help streamline communication and visibility between manufacturing, finance, sales and more — creating a lockstep rhythm that launches your company forward. The wrong one, or one that isn’t the right industry-specific fit, can muddy the waters and stunt your growth potential.
What makes an ERP the “right ERP”?
The “right ERP” should address the specific needs of a business beyond the out-of-the-box capabilities found in many basic ERP platforms. For example, in the case of craft brewers, it’s important to be able to correlate the capacity and functioning of the stages of the brewing process, ingredient sourcing, and the peculiarities of distributing craft beverages. These capabilities often require specialists to operate an out-of-the-box ERP solution, whereas an ERP designed for craft beverages would have these capabilities built in with customizable add-on modules to fit the brewery’s specific needs.
When evaluating different ERP systems, you want to look for a combination of solid baseline tooling, industry expertise, and flexibility to tailor the solution to meet the needs of your entire organization — from finance to the brewing floor. Let’s take a look at some criteria to help you find your perfect ERP match:
Industry expertise
If an industry-specific solution is a top priority for your company then there are two ways to get what your are looking for when it comes to ERP implementation. First, you could hire a specialist to build custom features inside a blanket ERP platform (like Netsuite). This is likely to be expensive and slow to bring into reality, and you will have to keep in mind that your industry expert may need to be kept on retainer or re-engaged contractually every time you need support or want additions or modifications.
The second option is to find a niche, pre-built ERP that has been configured for your industry and your specific application. This option is likely to be a faster one to get off the ground, as the solution has already been built with your specific industry in mind and with customizable options already available to be configured and added on. It is also likely that ongoing support and additions are likely a part of the package, or that managed services and ongoing customer care are something that can be added to your contract.
Solution for the entire organization
ERPs are unique applications in that they generally touch every facet of your organization from finance, to sourcing, to sales. Having a streamlined process where there is visibility into every step is important as companies begin and continue to scale. For example, when the business decision is made to begin distributing in a new region, there are multiple departments that need to be on board with the change. There may be new tax laws for your finance department to be aware of, new distribution channels that need to be developed, manufacturing schedules that need to be modified which bleeds into the need for potential new and different sourcing of raw materials.
When looking for the “right” ERP, you should make sure it not only has the expertise in specific areas like manufacturing and distribution, but it covers the basic functionality across the organization.
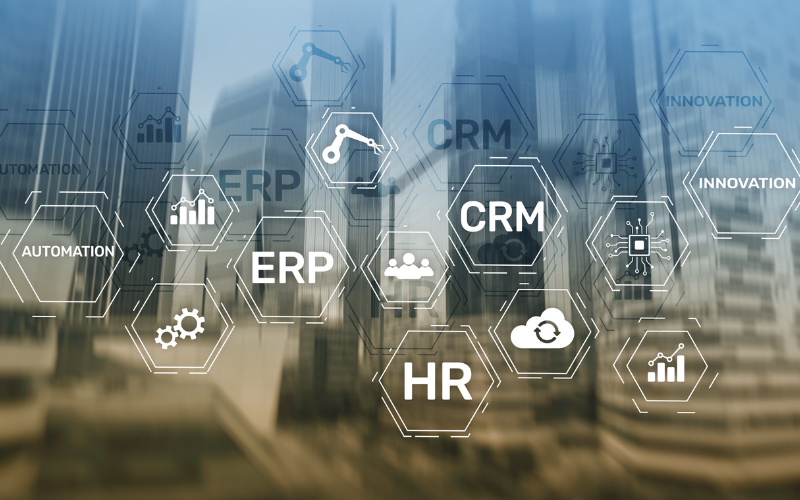
6 Benefits of choosing the right ERP for your brewery
Choosing the right ERP for your brewing operation can make or break your growth opportunities. By aligning all of your departments along your core goals with specific attention placed on your unique industry needs, your organization can move forward together in sync. Let’s take a look at some of the benefits that will be unlocked with the right ERP that offers the perfect combination of industry expertise and cross-organization capabilities.
1. Grow capacity without sacrificing quality
Not every brewing operation desires to scale beyond its initial objectives. There are many fantastic craft breweries that are content to remain regional powerhouses and serve happy customers for years to come. However, when a decision is made to expand in either volume, variety, or geography, breweries want to find a balance between nurturing that growth and maintaining their product quality and company integrity. The quality is what created the brand and keeps customers coming back — nobody is drinking your beer because of “how much” beer you produce. They keep coming back because of “how good” your beer is.
A suitable ERP that understands the brewing and distribution needs of your organization will allow all departments to grow together in a stable environment that will allow quantity to increase without sacrificing quality.
2. Implementation while minimizing stress on daily functions
Making organization-wide changes whether it’s new protocols, new reporting standards, or the introduction of new varieties of product, can cause stress on the already demanding daily functions of employees. Employees tend to resist sweeping organizational changes because they inject uncertainty into their day-to-day jobs. If new reporting requirements are all of a sudden a daily job to be done on top of current requirements, prepare for some internal strife.
The implementation of a new ERP platform has the potential to cause these types of problems. However, the introduction of new systems corresponding to the new platform in a stepped, gradual way is a key to
foster widespread adoption.
3. Implement branch-specific components
If a company has multiple branches, it’s likely that each branch will have specific requirements. The ability for an ERP to segment functionality for each branch may be a game-changing feature for your manufacturing and distribution operation. For example, local tax laws, distribution and shipping requirements, and fluctuating demands may vary depending on where the branch is located. The right ERP can streamline this process and make it easier for your business to pivot as needs change and evolve.
4. Real-time insight into the flow of goods
Real-time insight into the flow of goods is particularly important for craft brewing manufacturers. From the raw materials to the finished product, the flow of goods is a core consideration for running an efficient operation. This is where specialized configuration is so important for this industry. An out-of-the-box solution is not going to have the details required to track goods through the brewing process, but a custom solution for craft brewers certainly will.
This functionality is also important for departments like finance, operations, and manufacturing. Knowing where there are leaks in the process can be a critical insight to cost-saving decisions or uncovering potential sources of reduced quality in the process.
5. Improve quality control
Quality control is a fundamental part of making sure quality is not sacrificed when scaling the volume of a brewing operation. Having insight into an entire organization through a single pane of glass gives every department what it needs to ensure quality is not compromised.
As volume increases, distribution becomes more demanding, and new varieties are developed, the right ERP can make sure the proper departments have full visibility into the factors that go into keeping the quality to a brewer’s ideal standards.
6. Improve backend reporting and traceability
Reporting can be a headache. There’s no way around it. Being able to report on the success and failures of a system is nearly impossible when systems and monitoring capabilities are siloed to individual stages in the brewing operation. This is where a complete ERP solution comes into play. Having a clear view into the entire process makes reporting a breeze, and tracing problems to the specific stage of the process that is causing reduced quality or bottlenecks is easier with a single organizational system of record.
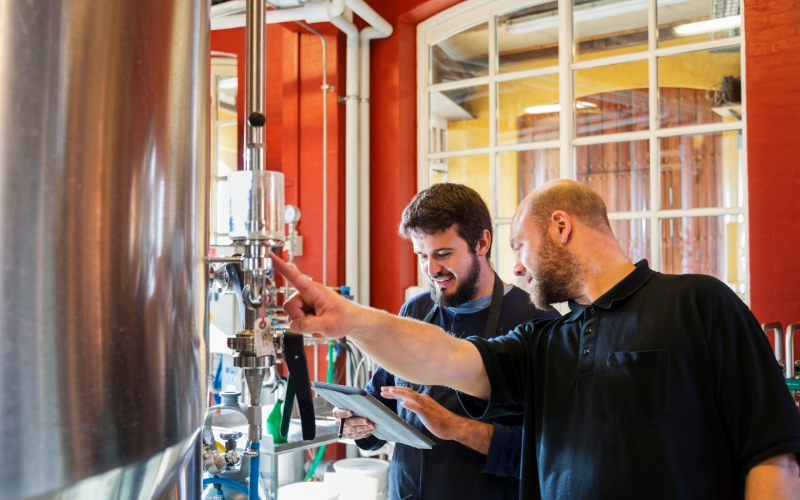
Key Takeaways
Choosing the right ERP requires a few core considerations. These include how to make sure sufficient expertise is injected into the ERP implementation, whether it is an expert specialist building custom functionality, or industry expertise built directly into the platform. The latter gives brewing manufacturers an enormous advantage with significant cost savings and reduction in onboarding time. Several benefits are unlocked when choosing a suitable ERP including the ability to increase quantity without sacrificing quality, changing business functions with minimal stress on day to day functions, the implementation of branch-specific features, real-time insights into the flow of goods, improved quality control, and easier backend reporting and traceability.